Why a Welding WPS is Crucial: Enhancing Consistency and Conformity
Why a Welding WPS is Crucial: Enhancing Consistency and Conformity
Blog Article
Understanding Welding WPS Requirements: Finest Practices and Techniques for Top Quality Welds
In the world of welding, grasping Welding Treatment Requirements (WPS) criteria is an essential component that directly affects the high quality and stability of welds. Abiding by these criteria makes certain consistency and dependability in welding outcomes. However, achieving quality in welds exceeds just recognizing the requirements; it includes executing best techniques and strategies that elevate the craft to a degree of precision and ability that distinguishes the average from the remarkable. As we navigate via the details of welding WPS requirements, revealing key insights and techniques for attaining top-tier welds will be vital for welders looking for to succeed in their craft and produce welds that stand the test of time.
Understanding Welding WPS Specifications
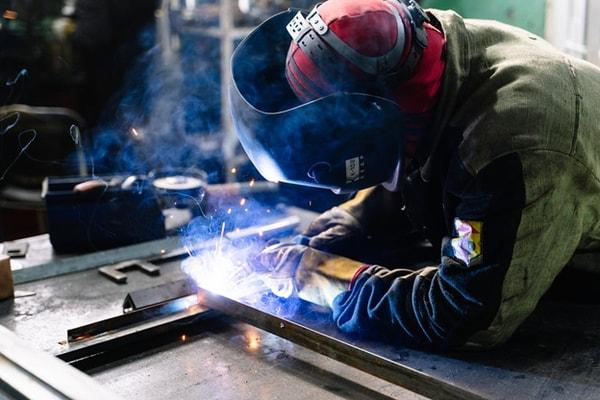
Inspectors count on WPS paperwork to validate that welding procedures are being adhered to appropriately and that the resulting welds are of high quality. Designers use WPS standards to make welding treatments that guarantee the durability and integrity of welded frameworks.
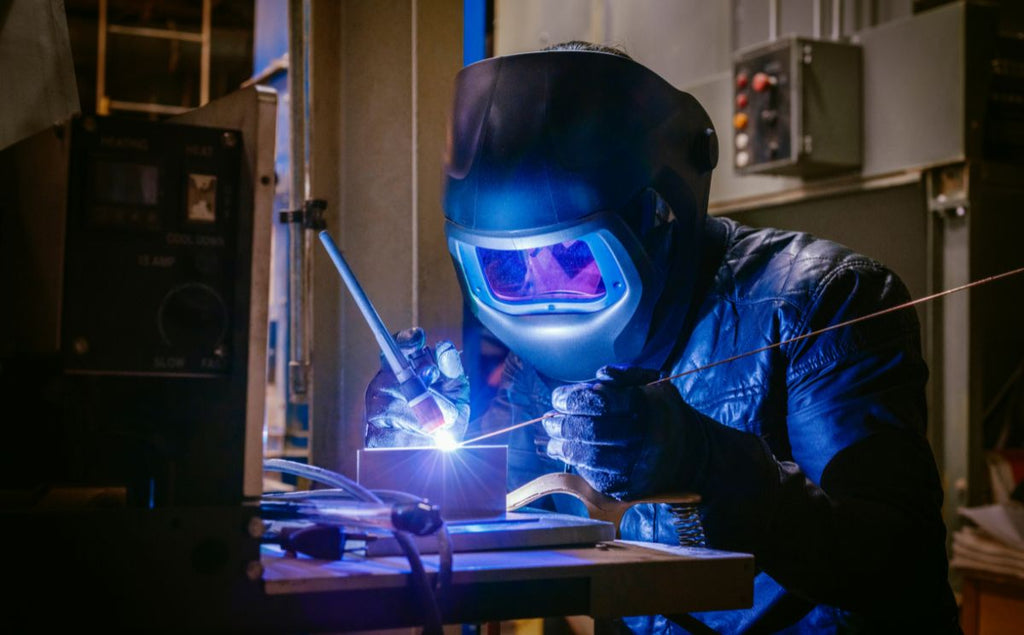

Crucial Tools for Top Quality Welds
Understanding welding WPS requirements is important for welders to successfully utilize the crucial tools needed for producing top quality welds. The kind of welding device required depends on the welding process being made use of, such as MIG, TIG, or stick welding. Wire brushes and damaging hammers are crucial for cleaning up the weld joint before and after welding to remove any kind of impurities that can affect the high quality of the weld.
Secret Methods for Welding Success
To achieve welding success, one have to grasp the vital methods vital for creating high-grade welds. One essential strategy is maintaining the right arc length. Maintaining the electrode at the optimum range from the work surface is vital for developing strong, consistent welds. Additionally, controlling the traveling rate is vital. Relocating also swiftly can result in inadequate infiltration, while relocating also slowly can lead to too much warmth input and prospective issues. Proper adjustment of the electrode angle is an additional crucial strategy. The angle at which the electrode is held can impact the bead shape and penetration of the weld. In addition, making sure constant weapon angle and instructions of traveling is more helpful hints essential for uniformity in the weld grain. Lastly, keeping a secure welding and a consistent hand placement throughout the process is crucial to achieving accuracy and consistency in the welds. By mastering these essential strategies, welders can elevate the high quality of their job and attain welding success.
Ensuring Conformity With WPS Criteria

In addition, welders should go through training to acquaint themselves with the WPS requirements relevant to their job. Routine audits and inspections should be conducted to verify that welding tasks line up with the recommended WPS guidelines. In addition, preserving detailed records of welding parameters, devices calibration, and assessment outcomes is critical for demonstrating conformity with WPS criteria - welding WPS. By diligently adhering to WPS requirements, welders can make certain that their work fulfills the required quality degrees and adds to the overall success of the welding task.
Troubleshooting Common Welding Issues
When confronted with common welding issues, identifying the source is essential for effective troubleshooting. One prevalent problem is the existence of porosity in welds, often created by contaminants such as corrosion, oil, or dampness. To resolve this, ensuring correct cleaning of the base metal before welding and utilizing the right protecting gas can dramatically reduce porosity. Another issue regularly experienced is lack of fusion, where the weld falls short to properly bond with the base product. This can come from insufficient heat input or improper welding method. Readjusting specifications such as voltage, wire feed rate, or travel rate can assist enhance fusion. In addition, distortion, fracturing, and spatter are typical welding obstacles that can be why not try here reduced via proper joint prep work, constant warm control, and picking the proper welding consumables. By thoroughly understanding these common welding concerns and their root creates, welders can efficiently repair troubles and accomplish top quality welds.
Verdict
In conclusion, understanding welding WPS criteria calls for a comprehensive understanding of the standards, utilizing vital tools, and implementing crucial methods for effective welds. Making certain conformity with WPS criteria is vital for generating quality welds and staying clear of usual welding concerns. By adhering to finest techniques and techniques, welders can achieve regular and trusted results in their welding jobs.
In the world of welding, mastering Welding Procedure Specification (WPS) standards is a crucial element that directly affects the quality and honesty of welds.When diving right into the realm of welding practices, a vital facet to comprehend is the value and ins and outs of Welding Procedure Specification (WPS) standards. WPS criteria offer an in-depth guideline for welding operations, ensuring uniformity, top quality, and safety in the welding procedure. The kind of welding device required depends on the welding procedure being utilized, such as MIG, TIG, or stick welding.Attaining welding success through the mastery of key methods demands a detailed understanding and adherence to Welding Treatment Requirements (WPS) criteria.
Report this page